When buying a used tractor front loader, basics will pretty much apply to all makes and models. All loaders tend to need the same basic checks, with key wear points pretty much in common. There are, however, a few Stoll specific considerations outlined here.
CONTROLLERS
Factory fitted loaders, to include those offered by Case, Deutz, New Holland and others share the same Stoll boom as offered by Stoll for its retrofit models, but the loader’s mounting brackets, controls and hydraulic valves will typically differ from Stoll’s own designs. The same will also apply to a tractor originally supplied from the factory as ‘loader ready’ as these too will have OEM controls and hydraulics. This is worth noting. Replacement joysticks, electronic controllers or valve chest components for OEM branded or ‘loader ready’ tractors could need parts specific to that brand or tractor model. All boom parts are, however, the same but it is always worth making contact with Stoll importers, Northants based Lynx Engineering, if you are unsure.
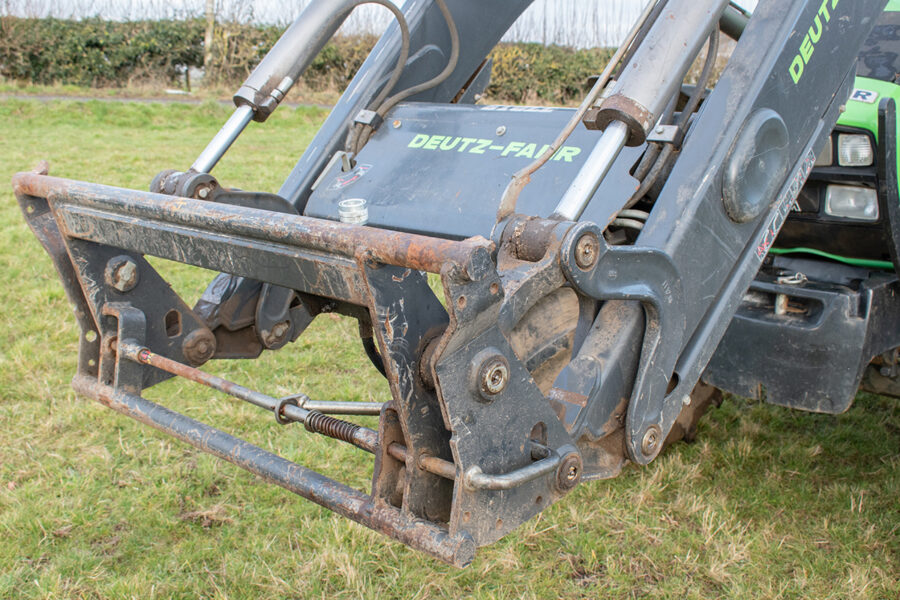
Stoll ProfiLine loaders will have been offered from new with a choice of mechanical cable operated joystick or electronic PRO Control. The latter can be retrofitted to replace an existing mechanical joystick and will work with both open and closed centre hydraulics. All the hydraulic and electrical connections are pre-installed on ProfiLine loader booms (but check with Lynx Engineering as there may be exceptions to include OEM branded loaders). TRAC Control, which essentially uses the same joystick as PRO Control, will fit in place of certain OEM armrest mounted proportional joysticks and again may be offered as a retrofit. Again, seek advice if this option looks like a viable upgrade.
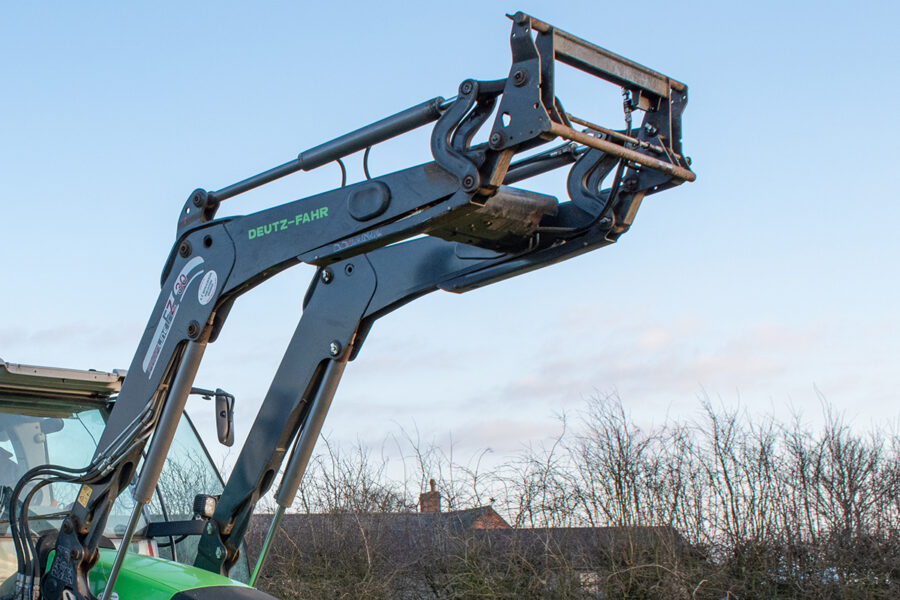
SOLID AND PROFILINE
From around 2012, Stoll divided its tractor loaders into two ranges, entry level Solid and higher specification ProfiLine. The Solid range, (previously Classic Line) will have reduced option and upgrade choices and are typically aimed at lighter tractors. ProfiLine (previously Robust) models are offered in FS and FZ variants, the latter featuring the Stoll Z-kinematics self-levelling system. This uses hidden beams to deliver parallel lift, doing away with visibility hindering over boom parallel rods. Comfort Drive boom suspension, with the damping system incorporated within the loader cross beam, and is an option on ProfiLine FS booms but is standard on the FZ variant.
Solid models can have a more basic entry-level spec, with features to include boom suspension listing as one of several options. This is an easy spot as the Solid system employs boom parallel control rods and an external accumulator adjacent to the lift ram.
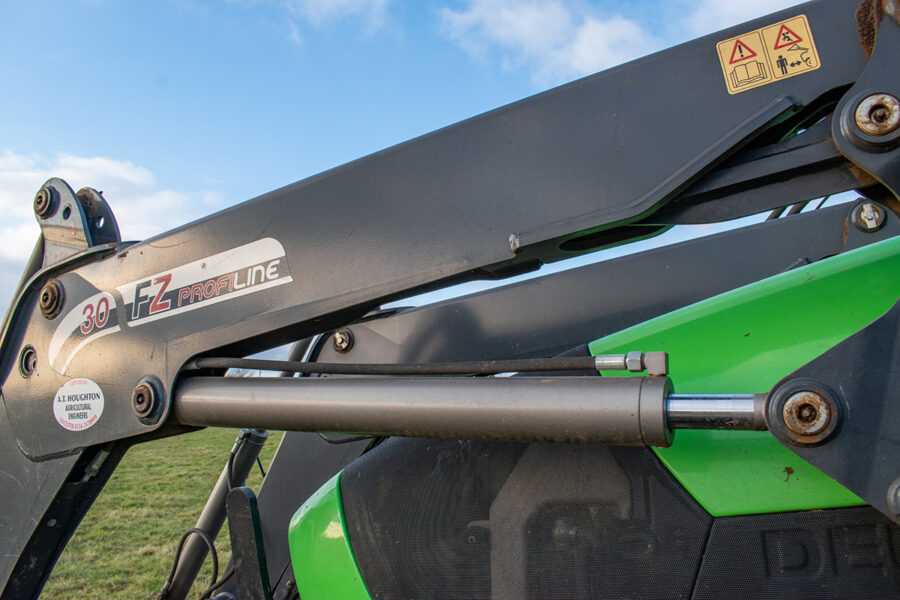
BASIC CHECKS AND POINTS TO NOTE (SEE PICTURE CAPTIONS FOR ADDITIONAL DETAIL)
Start at the headstock, looking for wear in the greaseable pivots and damage to the carriage. Most, but by no means all, Stoll loaders made in the last decade or so will have a standard Euro attachment carriage. Alternative carriages to suit dedicated attachments for loader makes to include Alö and MX are also available.
It follows that existing Euro attachments will fit a Euro carriage but a point on tilt and crowd angles. Bucket designs differ between loader makes and models, with Stoll OEM buckets having a back plate angle designed to ensure a fully crowded bucket is level and that the lower front plate angle will allow a clean dump at full tilt. Try and ensure a Stoll bucket comes with a used buy. Crowd and tilt angles vary between various Stoll loader models, with tilt angles of between 40 and 46 degrees at ground level and 69 degrees of crowd at full lift.
The Stoll attachment latch system is extremely simple, comprising a simple rod that is unlocked manually to release the attachment, but latches closed automatically. Replacement damaged latch parts to
include rods, roll pins, springs and washers are readily available. If possible, hitch on
an attachment to ensure it locks in place. Hydraulic unlocking from the cab is available as an option and is increasingly fitted to more recent loaders.
Stoll offers both individual hose and Hydro-Fix fast hydraulic connectors (with electrics where applicable). If separate hose connections are fitted, a retrofit conversion coupler kit is available for around £515 but be aware that Stoll switched to a revised Hydac valve block design in around 2015. A few connectors may need changing on older loaders to allow the kit to fit.
The loader’s serial number is to be found stamped on boom cross member and on a decal. This changed on newer models to a black metal plate located on the inner side of the left boom. This info can help identify the loader when pricing or ordering parts. The user manual and documents that came with the loader should help you identify the loader but if not, Lynx may well be able to help.
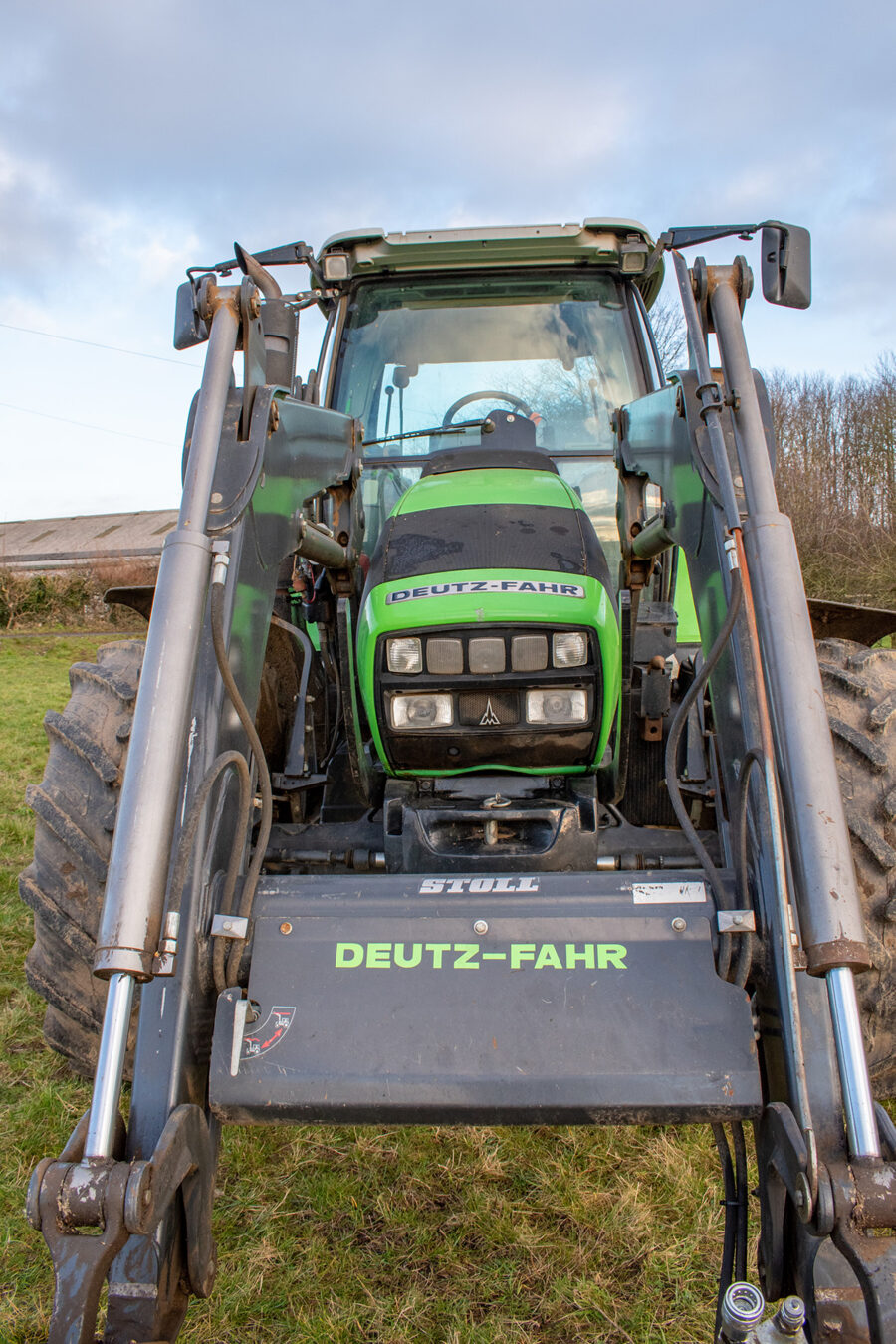
OTHER CHECKS
Weeping ram seals and oil leaks are obvious checks, as is pivot wear. The hardest working pivots are at the carriage end, but the lift ram and main boom pivots also need a good looking over. Ensure the pin locking tabs are in place, these simple bolt-on items occasionally coming adrift. If the tabs are missing, the pivot pin can ease out with pretty obvious problems as a result.
The crowd rams are tough but not immune to damage. Take a look to ensure the rams are not slightly bent through having been ‘abused’. They will still work with a slight ‘banana’ bend, but this will put a strain on the seals and pivots so will need further investigation. Easy to miss. Take a good look at the carriage linkage arms as these can get damaged too. New replacements are available.
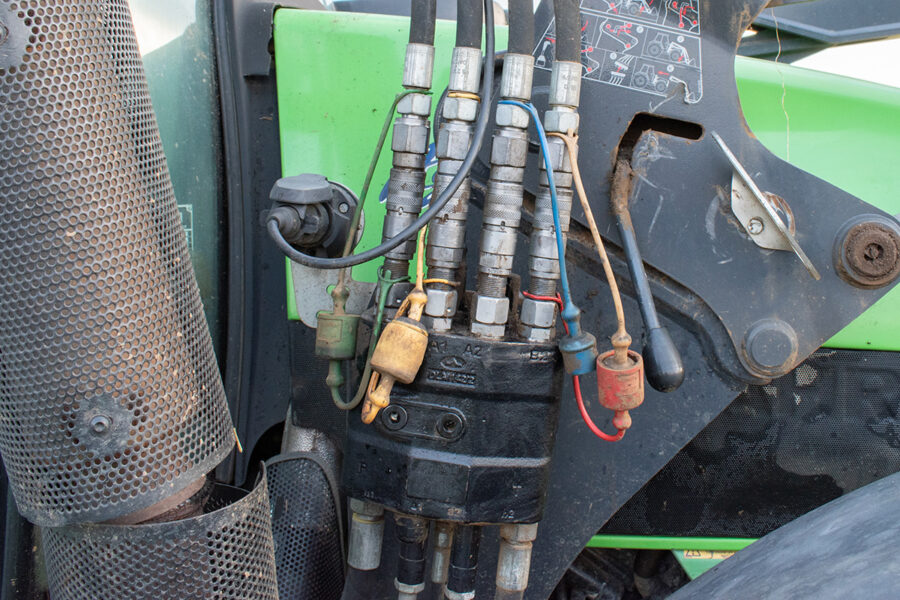
BOOM ATTACHMENT LEVER AND STANDS
Stoll developed its boom hook lock bracket attachment system back in 1983 and it has not changed since. The locking levers on each side of the boom need to be manually released and secured when removing and refitting the loader. The levers can become a little stiff on loaders that have not been removed in a while but should still shift with a small degree of effort. If the locking levers are stuck or really stiff, a squirt of release fluid into the locking mechanism’s Belville washers should be enough to free the latch. The mechanism can be adjusted, and a bent lever can be eased back into shape if it has been damaged in the past.
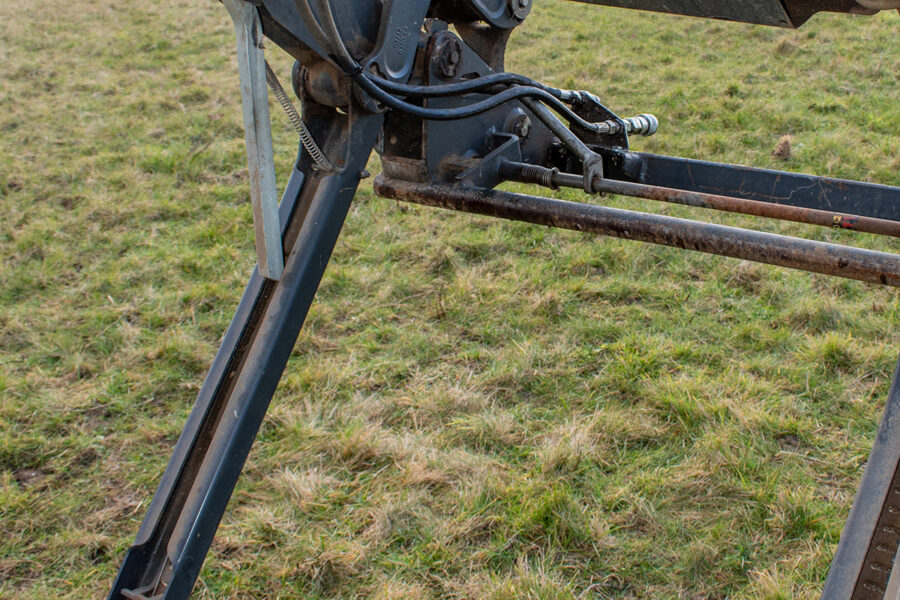
The loader stand legs are both fitted with a simple ratchet system that enables them to lock at an angle to cope with a moderately uneven surface. The legs and the catches that lock the legs in position are liable to damage. Lower each leg and ensure it locks when pressure is applied. Pulling the locking tab back will allow the leg to fold back and lock back in its stowage position on the boom. All the key parts to fix a damaged leg are available.
If you buy a tractor with Stoll or compatible OEM loader brackets fitted, but no boom, you may strike lucky and find a used one to fit. The snag is a boom that fits is not necessarily the correct one. Considerations should include its capacity, clearance to the front wheels and bonnet. It is easy to make a mistake. Stoll standardised on a wider boom for all tractors that are compliant with Stage IV / Tier 4 emission standards. Earlier loaders were offered in essentially two different widths to suit specific tractor models. Seek advice before assuming a used boom will fit.
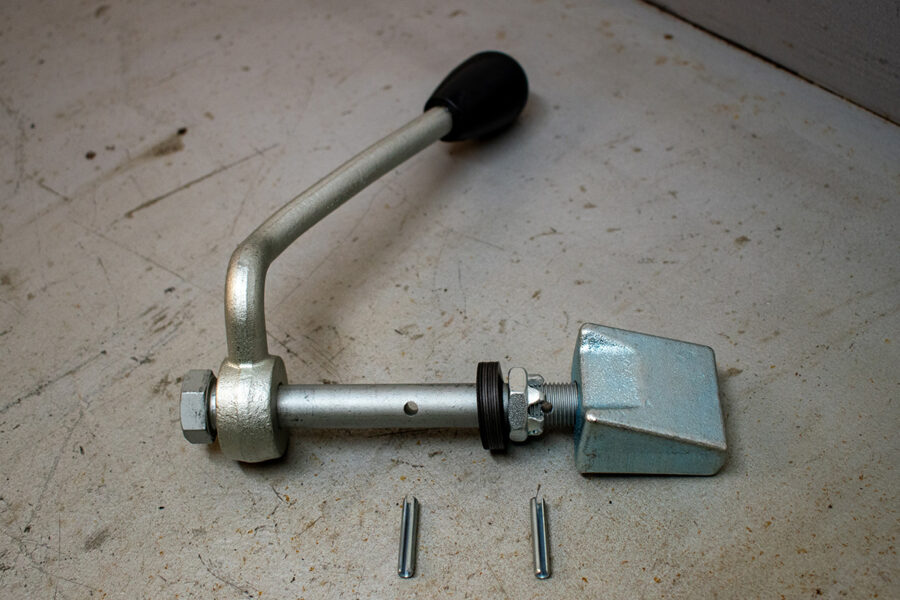
SUMMARY
When buying a used tractor with a loader, it is all too easy to overlook the loader itself.
As these bits of kit typically work hard and often see little in the way of TLC, it pays to invest some time giving them a good looking over. If the loader is not of the spec you want, a new loader boom is an option but consider affordable upgrades to the existing unit if it is just an upgrade to the controls you are after.
Later Stoll ProfiLine models, for example, can be affordably upgraded to electronic joystick control. A Stoll Solid loader with a worn and imprecise joystick need not be a problem either as these can be repaired or completely replaced relatively
QUICK KEY CHECKS
- Loaders tend to be abused and not given much care. A lack of grease in pivot points is common. The attachment carriage pivots are most liable to needing attention, so work back from here.
- Look for damage, and not just to the boom. The brackets and related fasteners are subject to shock loads, and the latter are meant to be checked regularly. Missing, snapped and damaged bolts are not rare on a non-dealer prepared buy. When greasing the loader, take a look at this area when a loader is in service.
- Mechanical joysticks wear can make it harder to work the loader smoothly and accurately. Lift the gaiter and look at the cable ball-ends to alloy plate socket. Play here can be rectified with a new plate.
- The mechanical joystick lock, mounted low down and on side, needs to be intact and fully working. Some knock it off and leave broken.
- Valve chest. Look for visible leaks. Leave the loader raised and check it does not sink. This can happen if there are internal leaks.
- Boom pin locking tabs can come loose, go missing or even break. If a pin tab is missing be wary. Other safety-related problems may be present.
- Boom cracks in ProfiLine and Solid loaders are rare. If you do see a crack or repair it suggests the loader has been abused.
- Level indicator rod provides a simple visual guide of the bucket level. Adjustable to suit different attachments, the level is mounted on the inner side of the left lift ram but it can be damaged or even lost. The thumb wheel adjuster lock can also loosen and fall off. Easy to fix with new parts.
- If ComfortDrive fails to engage initially, lower the boom for a few seconds and lift to relieve the back pressure in the system.
- The loader bracket lock handle should unlatch without undue force. If stuck, squirt in some oil and try again a bit later. Should free off easily.
- ElectronicPro-Control is fully digital. It should deliver linear control of the loader and attachments with good ‘feel’. The illuminated dots in the corner of each keypad decal will show if a certain function is switched on or off. Features such as boom suspension, third service, return to level, boom raise and lower speeds, sensitivity and more can all be programmed via the controller. Have a play to check. If the controller has a fault, it may need to be replaced as opposed to repaired.
- All Stoll mechanical joystick parts can be renewed to include the top decal and plastic handle components. OEM joysticks and controllers vary in quality and some have no repair parts; you have to replace the complete unit if it is worn or damaged. The third service buttons on some designs are known to fail so check.
- A StollHydro-Fix fast hydraulic connectors kit costs around £500 complete. Eases coupling under pressure.
- The tractor and its mounting brackets obviously need to match the loader. The Lynx website configurator can be used to check the boom and tractor are compatible.